195th ECS Meeting | Seattle, WA | May 3, 1999
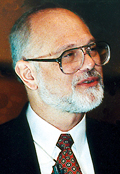
Aerospace Materials for the 21st Century
Aerospace Materials for the 21st Century
Dr. Alan G. Miller of the Boeing Co. gave the plenary lecture entitled “Aerospace Materials for the 21st Century.” A Boeing veteran of 20 years, he is currently the Chief Engineer of Boeing materials technology and is responsible for the corporate materials laboratory. His technical management responsibilities pertain to all materials and processes used in the commercial airline group products. These include R&D, design analysis, production and fleet support, and performance management. Following are excerpts of his talk in Seattle.
The electrochemical, and more generally, materials-related challenges in the aircraft industry can be broken down into three categories: near-term challenges include chrome-free and cadmium-free plating formulations and coatings. In the intermediate category would be the development of durable, regenerative passivating films for high-strength aluminum and steel alloys. Finally long-term developments would include active, conformal surface shaping for aerodynamics; smart surface films that facilitate in situ corrosion monitoring; and tailorable surface finishes on the aircraft exterior that would facilitate, for example, on-demand and reversible alterations in logos and visual appearance. The last-named application addresses the projected trend in the airlines industry of sharing of infra-structure and support systems. Thus it is conceivable and intriguing that a passenger boards an Air Canada jet in North America and then lands in a Lufthansa carrier in Europe!
The drivers for materials development are range, fuel consumption, aging, and fare with the three figures of merit being performance, maintenance, and cost. The new Boeing 777 aircraft features new alloys and composites derived from Al (70%), steel (11%), titanium (7%), composites (11%), and miscellaneous (1%). Problems with current-generation materials were discussed including the rather poor corrosion-resistance of Al alloys coupled with the cost and weight of Ti alloys. New materials are sought that combine high fracture toughness with yield strength.
Corrosion prevention is another crucial area in aerospace technology that directly impacts on the electrochemical community. Current goals in this area revolve around Alodine replacement coatings because of the environmental concerns with hexavalent chrome. Two such new-generation coatings were discussed, namely cobalt conversion coating and another conversion coating based on the solgel approach. A third coating under development is a tungsten carbide-cobalt thermal spray formulation specifically for landing gear applications.
A unifying theme in Dr. Miller’s talk was how aerospace materials provide an example of the benefits of an integrated-technology approach where materials science/engineering, corrosion science, and chemistry all contribute in a synergistic manner to provide effective solutions to commercial demands.