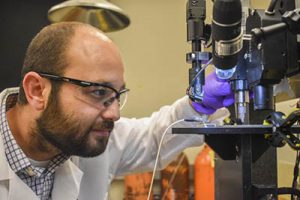
Arda Gozen, assistant professor, WSU School of Mechanical and Materials Engineering. Photo Credit: WSU
Living with any disease isn’t easy. In particular, when it comes to living with diabetes, it involves an imposed routine of finger pricking and monitoring of glucose levels in order to simply maintain a healthy lifestyle. So you can imagine, any technology that can ease the sting is welcomed. Researchers at Washington State University have developed a 3D‑printed glucose biosensor for use in wearable monitors that may forever change how millions monitor their glucose levels.
According to Futurism, the research team—led by Arda Gozen and Yuehe Lin—have developed 3D-printed sensors that could stick to a person’s skin and monitor glucose via bodily fluids, like sweat. The 3D-printed glucose monitor offers much better stability and sensitivity than those manufactured through traditional methods, according to Washington State University. In addition, compared to traditional manufacturing processes, these 3D-printed sensors also cut down costs and reduce waste like expensive cleanroom processing and harmful chemicals. (more…)