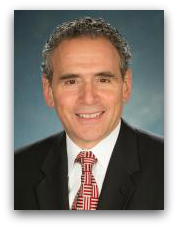
Gerald Frankel, a technical editor of the Journal of The Electrochemical Society, corrosion expert, and open access advocate.
The aftereffects of the Flint water crisis is still felt strongly four years later. Just this year, dozens of Flint, Michigan, residents were outraged by the state’s decision to end a free bottled water program. A program that came into effect after it was discovered the water in Flint was unsafe for consumption.
The catastrophe came to fruition when measures were taken by elected officials to cut costs. The result of which led to tainted drinking water that contained lead and other toxins.
Gerald Frankel, a professor of materials science and engineering at The Ohio State University, touched on the matter in an ECS Podcast interview.
“It was avoidable,” says Frankel, who explained that because water is corrosive, drinking water is treated to reduce the corrosive effects on the pipes that carry it. However, due to financial issues the town of Flint was facing, their source of the water changed from Lake Michigan to the Flint River. “And they decided not to do this chemical treatment.”