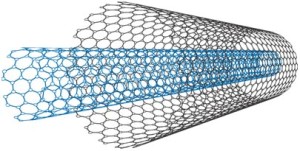
Carbon nanotubes are exceptionally strong, but when you roll two that fit together, the engineers believe they’ve got a nanomotor.
Image: Nature
Ray Kurzweil – an author, computer scientists, inventor, futurist, and director of engineering at Google – has once been quoted saying, “In 25 years, a computer that’s the size fo your phone will be millions of times more powerful but will be the size of a blood cell.”
That prediction may be on its way to fruition with this new discovery from engineers in China and Australia.
The engineers have developed a double-walled carbon nanotube motor, which could be a huge player in future nanotechnology devices.